Maintaining filter efficiency in irrigation systems
When discussing filter efficiency, the focus has always been on the size of the filtration area, or effective filtration area. This area is defined as the total area of the filter medium exposed to the water flow and which participates in the filtration process. To understand that filter efficiency is about much more than the size of the filtration area, let’s talk about how we define disc filter efficiency.
Conventionally, effective filtration area is discussed in a two-dimensional context. However, when it comes to disc filtration we should change to a three-dimensional way of thinking.
Remember, disc filtration, like media filtration, is multi-layered and offers depth filtration. This means there are second, third and successive chances to catch a particle in subsequent layers.
Disc filters consist of a cylinder of compressed discs. Each disc has grooves that run in alternate directions that criss-cross when two discs are placed on top of each other, forming a series of meshes. These grooves form passages of varying dimensions through which the water passes from the outside to the inside of the discs. Water is filtered as it enters the cylinder of compressed discs from the outside to the inside.
The number of layers depends on the selected micron rating of the discs. In the case of Netafim disc filters’ unique disc design, there can be between 18 (for 400-micron discs) and 32 (for 20-micron discs) layers or stopping points in each track, resulting in unique depth filtration.
Click here to read more about filter types and selection.
Considering this technical explanation of how a disc filter functions, it is clear why we could look at disc filtration as three dimensional. However, how do we measure a three-dimensional filtration element? The answer is dirt holding capacity (DHC).
A filter’s DHC represents the number of particles (mg) retained on the filter medium during a single filtration cycle. This concept can be expressed as the following mathematical equation: Backwash total suspended solids (mg/l) x backwash volume (L) = DHC (mg).
The DHC of a filter will vary based on the filtration technology type used (surface or depth), water source quality (type of particles), working conditions (filtration velocity – Q/A, dP) and the filter element structure (porosity, depth, surface properties, construction material).
The DHC will determine a filter’s backwash frequency and efficiency, which determines filtration efficiency. A higher DHC means fewer backwash cycles as the filter can hold more dirt particles per square centimetre. In addition, fewer backflush cycles save water and energy.
If a filter’s backflushing cycle is inefficient, it will not only require more frequent backflushes; dirt will also accumulate on the filter over time. This will eventually limit the filter’s ability to function, require manual cleaning and interrupt irrigation. If the filter does not revert to the initial head loss after a cleaning cycle, it means the filter’s backflush efficiency is low. This, of course, will reduce the DHC and increase the backflush frequency. If this inefficient backflush cycle continues, you will have to manually clean the discs more often.
The graph below describes the importance of low, stable head loss. The filter shown by the blue line has a lower DHC compared to the filter shown by the red line.
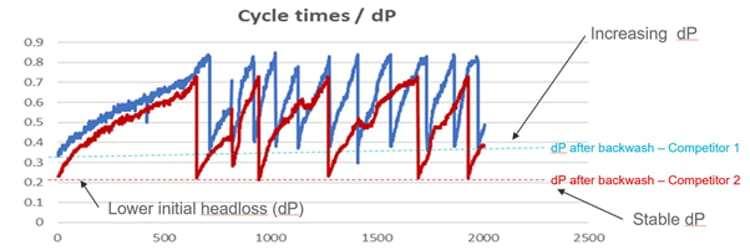
A filter should not be judged by its effective filtration area alone. In the field, the filters compared above are both disc filters with similar filtration areas. However, there is a significant difference in how they respond in terms of backflush frequency and head loss maintenance.
Maintain efficiency
Whichever way efficiency is calculated, it cannot be maintained without proper and regular maintenance of the filter. Without it you will most likely encounter problems, and the filter will fail to protect the irrigation system all year.
A filter maintenance schedule can be divided into three sections:
- Weekly maintenance.
- Maintenance at the end of the irrigation season.
- Maintenance at the start of the irrigation season.
Screen filter maintenance
It is important to conduct weekly visual inspections on automatic, semi-automatic and manual screen filters. The main purpose of these inspections is to check for leaks, which should be repaired as soon as possible.
If you are working with an automatic screen filter and you have found no leaks, activate a manual flushing cycle to ensure the filter is flushing successfully. The next step is to check the pressure differential. If this value is abnormally high, perform two more manual flushing cycles. If the value remains high after three manual flushing cycles, the filter should be opened, checked for failed parts and the screen cleaned manually if necessary.
Be sure to follow the manufacturer’s step-by-step guide and all safety instructions when opening the filter and taking out the screen. To clean the removed screen, use pressurised water to remove the remaining dirt. Reinstall the clean screen according to the supplier guidelines and follow all safety instructions.
In a semi-automatic screen filter, the cleaning operation must be initiated before the pressure differential reaches 0,5 bar. Some semi-automatic screen filters have an automatic clogging indicator that will communicate when the pressure differential limit is reached.
To initiate the cleaning operation, open the drain valve and turn the handle all the way out and then back in. The screen’s inside will be cleaned as you turn the handle and suction is created in the nozzles. If you are working with poor water quality or low pressure, it is advisable to perform the cleaning operation while the downstream valve is closed. Close the drain valve after the process has been completed.
If the pressure differential remains abnormally high after three completed cleaning operations, the filter should be opened, checked for failed parts and the screen cleaned manually if necessary.
In a manual screen filter a high-pressure differential will always require opening the filter for manual cleaning. Start by closing the water supply to the filter and opening the drain valve to release all the pressure. Open the filter body clamp and remove the filter cover. Carefully pull out the screen element and clean it using pressurised water. If necessary, use a soft nylon brush for more efficient cleaning. Never use any abrasive tools and make sure the body and screen O-rings are lubricated before reassembly.
Disc filter maintenance
The filter should regularly undergo a general inspection. It should also be inspected before any scheduled maintenance procedures are carried out.
Check the pressure differential between the filter inlet and outlet. Then initiate a flushing cycle and recheck the pressure differential a minute after the flushing cycle has been completed. If the pressure differential is still abnormally high, you will need to open the filter and remove the discs for manual cleaning. Before removing the filter cover, close the water supply to the filter and open the drain valve to release all the pressure.
Visually inspect the discs after they have been removed. If there is visible sediment, clean the discs according to the supplier recommendations. Furthermore, visually inspect the spine and make sure the cone membrane is not damaged. If any filter parts are damaged, replace them immediately.
When reassembling the spine and discs, make sure the number of discs is correct, as indicated by the line on the spine, and lubricate the O-rings. Also, open the command filter and clean its discs.
Media filter maintenance
As is the case with disc and screen filters, it is important to inspect a media filter regularly. This type of filter generally consists of crushed basalt or graded silica sand. For successful filtration, the media must be angular with sharp edges to provide the best environment for trapping debris. The media must be replaced as soon as the edges become rounded from wear, so check it regularly.
During the inspection of a media filter, check the pressure differential between the system inlet and outlet. Check the accumulating number of flushes since the last inspection to see if water quality is deteriorating. Initiate a manual flush and check for proper operation and sequence. After the manual flush is completed, check that the sand level in each tank matches the media-level indicator. In addition, be sure to clean the check filter.
Netafim’s Precision Irrigation Academy has published several informative videos on filter maintenance and other important activities. Click here to watch these videos.
Choose the best and look after it
Various factors determine the success of an irrigation system, of which filter selection and setup is but one aspect. To ensure that a filtration system keeps functioning effectively and has a long lifetime, two factors should never be neglected: the use of quality products and system maintenance. In terms of product quality, the message is clear: You cannot afford to risk the financial viability of your project by not investing in the best possible irrigation equipment.
With regard to maintenance, be sure to take the right actions at the right time to ensure efficiency is maintained and filters perform at their full potential.
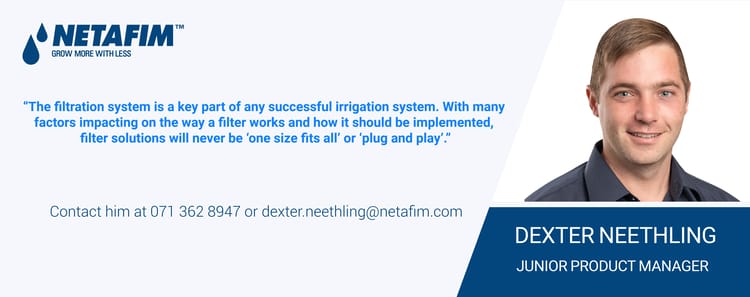
Share your thoughts
Comments
We'd love to hear your thoughts! To enter a comment, type your name and email address.